What is Tablet Capping and How to Avoid It
Tablet capping is a common issue during tablet production where the top or bottom part of a tablet separates or breaks off. It can lead to wasted materials, production delays, and poor-quality products. This article explains what causes capping and how to fix or prevent it. Whether you're new to tablet manufacturing or troubleshooting a recurring problem, these tips can help keep your tablets intact and your production on track.
Tablet Capping Definition
The term tablet capping is used when either the upper or lower part of the tablet separates horizontally either partially away from the main body or completely to form a cap when ejected from the press or during the handling process.
Sign Up to Our Newsletter
Common Causes and Fixes for Tablet Capping
Tablet capping can happen for a few different reasons, but most of the time, it comes down to either formulation issues or problems with the tablet press. The tables below break down common causes from both sides—what’s happening with the powder or granules, and what might be going wrong with the machine. For each issue, you’ll also find a practical fix.
Formulation-Related Tablet Capping Causes and Solutions
Cause | Solution | |
1. | Large amount of fines in the granulation | Remove some or all fines through 100 to 200 mesh screen |
2. | Too dry or very low moisture content (leading to loss of proper binding action). | Moisten the granules suitably. Add hygroscopic substance e.g.: sorbitol, methyl- cellulose or PEG-4000. |
3. | Not thoroughly dried granules. | Dry the granules properly. |
4. | Insufficient amount of binder or improper binder. |
Increasing the amount of binder OR Adding dry binder such as pre-gelatinized starch, gum acacia, powdered sorbitol, PVP, hydrophilic silica or powdered sugar. |
5. | Insufficient or improper lubricant. | Increase the amount of lubricant or change the type of lubricant. |
6. | Granular mass too cold to compress firm. | Compress at room temperature. |
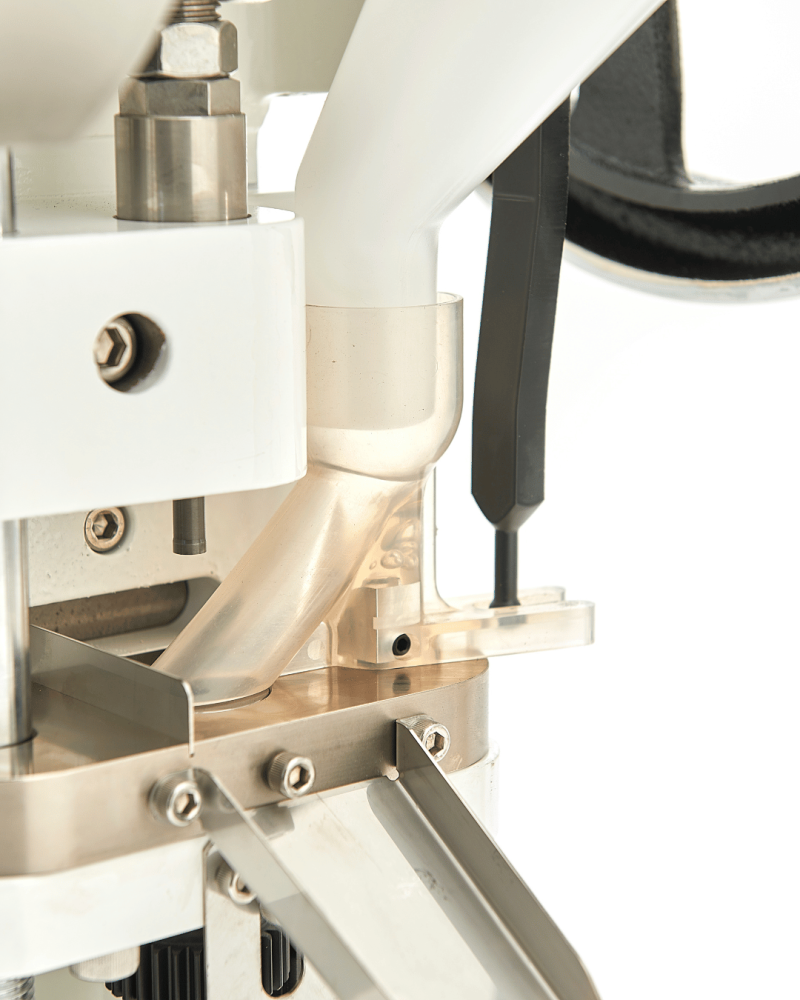
Machine-Related Tablet Capping Causes and Solutions
Cause | Solution | |
1. | Poorly finished dies | Polish dies properly. Investigate other steels or other materials. |
2. a |
Deep concave punches or beveled-edge faces of punches. | Use flat punches. |
3. | Lower punch remains below the face of die during ejection. | Make proper setting of lower punch during ejection. |
4. | Incorrect adjustment of sweep-off blade. | Adjust sweep-off blade correctly to facilitate proper ejection. |
5. | High turret speed. | Reduce speed of turret (Increase dwell time). |
Tablet capping is a frustrating but fixable problem. Whether it's due to your formulation or how your machine is set up, identifying the cause is key to getting consistent, high-quality tablets. The tips in this guide can help you spot the issue and take the right steps to fix it.
If you're still running into problems or want expert advice, contact LFA Machines. We're here to help you find the right tableting solutions for your process.