Tablet defects occur for a variety of reasons, but many can easily be avoided. To address defects, technicians involved in tabletting must have a full understanding of both the tabletting process and the materials used. Adequate training in the setting up and use of the machines is vital if the technician is to have the necessary skills to be able to fix equipment and minimize problems in production.
Tablet Binders
Tablet Binders Key Points
-
Role of Tablet Binders: Tablet binders, also known as adhesives, are crucial in tablet formulation. They promote cohesiveness, helping ingredients mix together and converting powders into granules through granulation.
-
Importance of Granulation: Granulation enhances powder properties, ensuring tablets have consistent weight, uniform strength, and remain intact under pressure. It also improves appearance, reduces dustiness, and enhances mixing properties.
-
Types of Binders and Processes: Binders are categorized into sugars (e.g., sucrose), natural binders (e.g., acacia), and synthetic/semi-synthetic polymers (e.g., methyl cellulose). The two primary granulation methods are direct compression, using directly compressible binders, and wet or dry granulation, where binders are added in solution or suspension form.
Tablet binders are one of the most essential elements in the formulation of a tablet. Because they promote cohesiveness, the binders, also called adhesives, help the other ingredients in a tablet to mix together. Tablet binders are used to turn powder to granules; this is achieved through the process of granulation. During granulation, powder substances are accumulated to form larger particles called granules.
Why is Granulation Important for Tablet Binders?
When powdery particles or granules are intended for compression into a tablet, they must have two important properties:
- Flow property – tablets should be a consistent weight and uniform strength
- Compressibility – tablets should remain intact, compact, and stable, even when pressure is applied
Before undergoing the granulation process, these properties can be achieved by adding binders to the formulation. Binders should be utilized if a tablet displays poor fluidity and compressibility.
Aside from the methods mentioned above, granulation can also help to achieve the desired tablet appearance, avoid dustiness, improve mixing properties, decrease segregation, eliminate undesirable properties, and finally, to improve the physical and chemical properties of the powder.
Iscriviti alla nostra newsletter
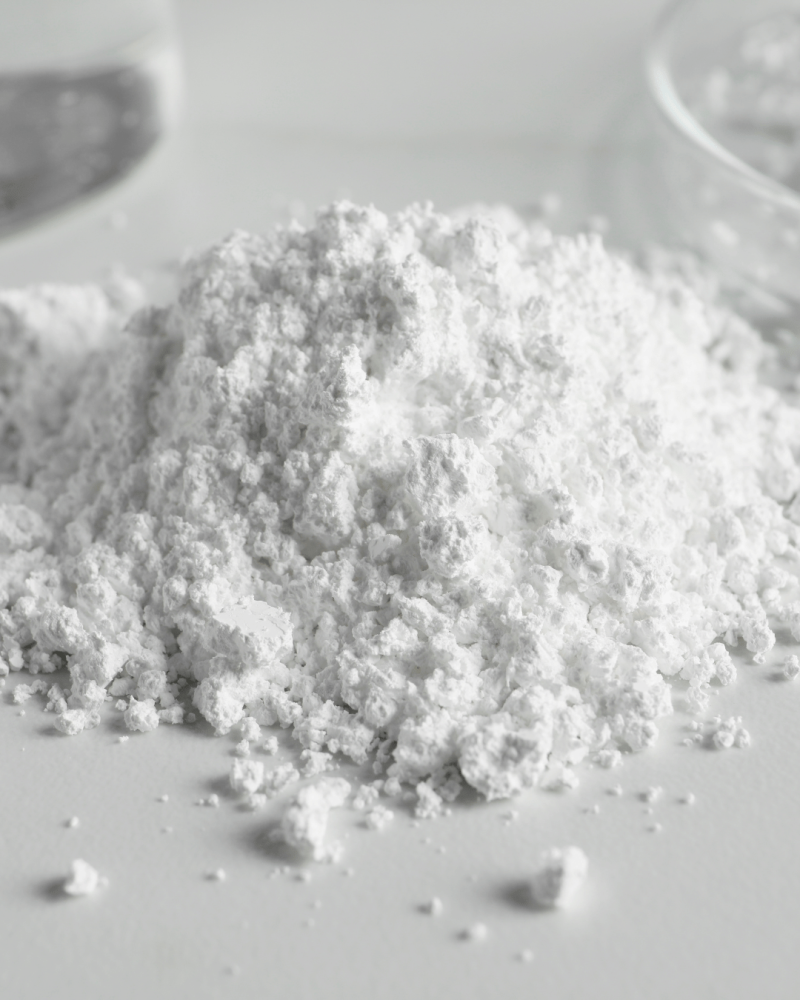
Processses for Tableting Binding & Granulation
The two most common methods used in the tableting industry are: direct compression and granulation. Direct compression, as the name suggests, involves using the binders that have direct compressibility. The liquid form of the binder is more effective than those in dry form. Granulation on the other hand, involves the use of wet and dry granulation; here, binders in solution or suspension form are added.
Classification of Tablet Binders
Sugars | Natural Tablet Binders | Synthetic/Semisynthetic Polymer |
Sucrose | Acacia | Methyl Cellulose |
Liquid glucose | Tragacanth | Ethyl Cellulose |
Gelatin | Hydroxy Propyl Methyl Cellulose ( HPMC) | |
Starch Paste | Hydroxy Propyl Cellulose | |
Pregelatinized Starch | Sodium Carboxy Methyl Cellulose | |
Alginic Acid | Polyvinyl Pyrrolidone (PVP) | |
Cellulose | Polyethylene Glycol (PEG) | |
Polyvinyl Alcohols | ||
Polymethacrylates |
Commonly Used Tablet Binders
Tablet Binder | Category | Manufacturer |
Starch 1500O | Partially Pregelatinized Maize Starch | Colorcon |
MethocelO | Hydroxy Propyl Methyl Cellulose | Dow Chemicals |
WalocelOHM | Hydroxy Propyl Methyl Cellulose |
|
LuvitecO | Polyvinylpyrrolidone | BASF Company |
LuvicrossO | Polyvinylpyrrolidone | BASF Company |
LuvicaprolactamO | Polyvinylcaprolactam | BASF Company |
Characteristics Of Commonly Used Tablet Binders
Tablet Binder | Specified Concentration | Comments |
Starch Paste | 5-25%w/w |
|
Pregelatinized Starch (PGS) [Partially and Fully PGS] |
5-10%w/w (Direct Compression) 5-75%w/w (Wet Granulation) |
|
Hydroxypropyl Methyl Cellulose (HPMC) | 2-5%w/w |
|
Polyvinyl Pyrrolidone (PVP) | 0.5-5%w/w |
|
Polyethylene Glycol (PEG) 6000 | 10-15%w/w |
|
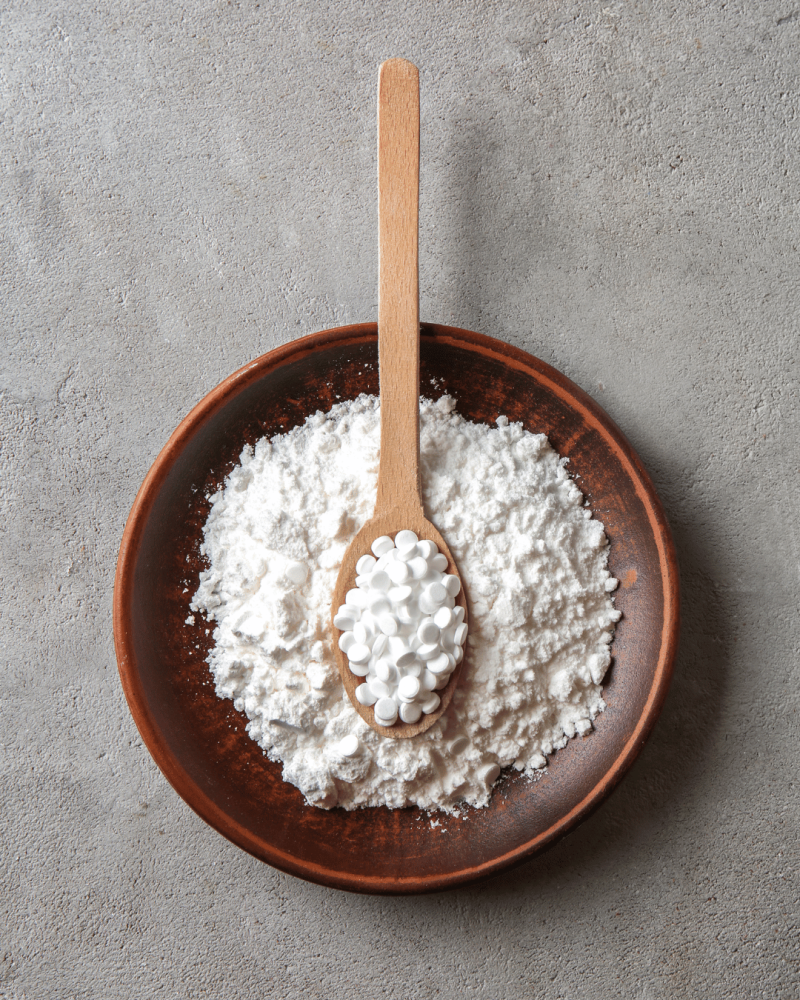
Direct Compression Tablet Binders
Direct Compression is an easy, efficient method in manufacturing that provides a stable product; as such, it is increasing in popularity. The process involves using directly compressible binders that have high flowability and compressibility. In order to obtain optimum binding performance, manufacturers must use direct compression binders that have excellent volume reduction when under applied pressure and should also base selection on the compression and flow behavior. These factors are particularly important for Direct Compression tablets.
Commonly Used DC Tablet Binders
DC Tablet Binder | Class | Manufacturer |
AvicelO (PH 101) | MCCa | FMC Corporation |
SMCCO (50) | SMCCb | Penwest Pharmaceutical |
UNI-PUREO(DW) | Partially PGSc |
National Starch & Chemical |
UNI-PUREO (LD) | Low density starch | National Starch & Chemical |
DC LactoseO | DC lactose anhydrous | Quest International Group |
DI TABO | DC-DCPDd | Rhodi |
a - Microcrystalline Cellulose, b - Silicified Microcrystalline Cellulose, c - Pregelatinized Starch, d - Dibasic Calcium Phosphate Dihydrate
Characteristics Of DC Tablet Binders
Flow Behavior | DI TABO> SMCCO(50) > DC LactoseO , UNI PUREO(DW) > AvicelO (PH 101) > UNI PUREO(LD) |
Compressibility | UNI PUREO(LD) > SMCCO(50) , AvicelO(PH 101) > UNI PUREO(DW) , DC LactoseO > DI TABO |
Crushing Strength | UNI PUREO(LD) > SMCCO(50) > UNI PUREO(DW) > AvicelO(PH 101) > DC Lactose O> DI TABO |
Granule Formulation Stages for Tablet Binding
- Nucleation
- In this stage, the particles stick to one another due to the liquid bridges. The particles that form serve as the nucleus of the granule.
- Transition
- This stage involves the enlargement of the nucleus either by other particles sticking to the nucleus or several nuclei combining together.
- Enlargement
- The granules form a ball shape and grow in size due to one of several processes: (a.) Coalescence, where two or more granules unite into one (b) Breakage, where some granules break and adhere to other granules (c) Aabrasion, where abraded materials and other granules in the granule bed stick to the formed granule through agitation of the bed. (d) Layering, where particles stick to the formed granule Near Infrared Spectroscopy (NIR) - Measuring Granulation End Point NIR is used to monitor the wet granulation process when the impeller torque is not used. The end point for granulation has been determined using
agitated fluidized bed. The IR sensor is installed and the wet mass properties are obtained independent of the impeller method. The NIR can also be used to
measure powder blending efficiency during the dry mixing phrase but is more ideal for measurement in the wet granulation process.
- The granules form a ball shape and grow in size due to one of several processes: (a.) Coalescence, where two or more granules unite into one (b) Breakage, where some granules break and adhere to other granules (c) Aabrasion, where abraded materials and other granules in the granule bed stick to the formed granule through agitation of the bed. (d) Layering, where particles stick to the formed granule Near Infrared Spectroscopy (NIR) - Measuring Granulation End Point NIR is used to monitor the wet granulation process when the impeller torque is not used. The end point for granulation has been determined using
Tablet Binder Factors to Be Considered:
- Compatibility: Compatibility of the binder with other components is very important. The Differential Scanning Calorimetry can be used to determine compatibility.
- Drug Characteristics: Characteristics such as size, porosity, compressibility, solubility and hydrophobicity can affect the process. Drugs that have poor compressibility would require strong binders whereas porous ones would need a high level of liquid binder. Drugs that have high absorption rate would require higher volume of binder.
- Spreading of the Binder: Spreading the binder together with the powder blend is another important factor; an excellent binder is one that can be easily spread (e.g. HPMC).
- Binder Quality and Type: The uniformity of the tablet's features depends on the quality of the binder added to the formulation. A high concentration of binder can cause hard granulation, whilst insufficient quantity of the binder would result to fragile granulation. Large quantities of granulating liquid can cause coarse and hard granules. In order to ensure that variations are limited and uniformity is reached, the quantity of the liquid added should be prepared and measured beforehand.
- Temperature and Viscosity: Less viscous binders should result in better spreading.
- Method of Adding Binders: The way binders are added is also important. PVP, can be used as a dry or liquid solution when being added to the formulation. It is better to disperse the binders than to pour directly into the mix.
- Mixing Time: The quality of the granules may also be affected by the mixing time. If the wet mass time is higher, this would result in hard granules, and in turn, the tablet failing the dissolution test because the drug release time is altered.
- Granulator Construction Materials: The type of construction material affects the volume of the binder and the granule size being distributed. Vessel walls that are wetted easily by binders would require a high volume of binders; for example, stainless steel vessels would require higher binder volume than vessels that are made of plastics such as PMMA or Teflon. The use of PMMA or PTFE would narrow the particle size distribution due to the high contact angle whereby all liquids are forced directly to the powder bed. With stainless steel, this is different: less contact angle liquid layer is formed in the wall surface, causing inhomogeneous distribution of the liquid over the powder bed, resulting in broader granules.
- Granulator Type: Fluidized bed granulators produce porous granules unlike those produced by the High Shear granulator.
- Variable Process: Higher impeller speed and longer wet massing time can affect the size of the granules. Agglomeration can also occur due to an increase in liquid saturation time.
- Variables Apparatus: The apparatus used can affect the growth of the granules. Using the High Shear Mixer will result in larger granules than using Fluidized Bed Granulators; this is due to the construction of the mixer. The shape, size chopper, and impeller of the mixing chamber are different in each apparatus.
- Impeller Movement: Wet mass sticks to the vessel less if the impeller movement is helical, resulting in fewer lumps and narrow granule size. This is usually a problem when using the High Shear Mixers because wet mass sticks to the vessel; coating the vessel with polytetrafluoroethylene can reduce this problem. The correct construction of the impeller must also be observed.
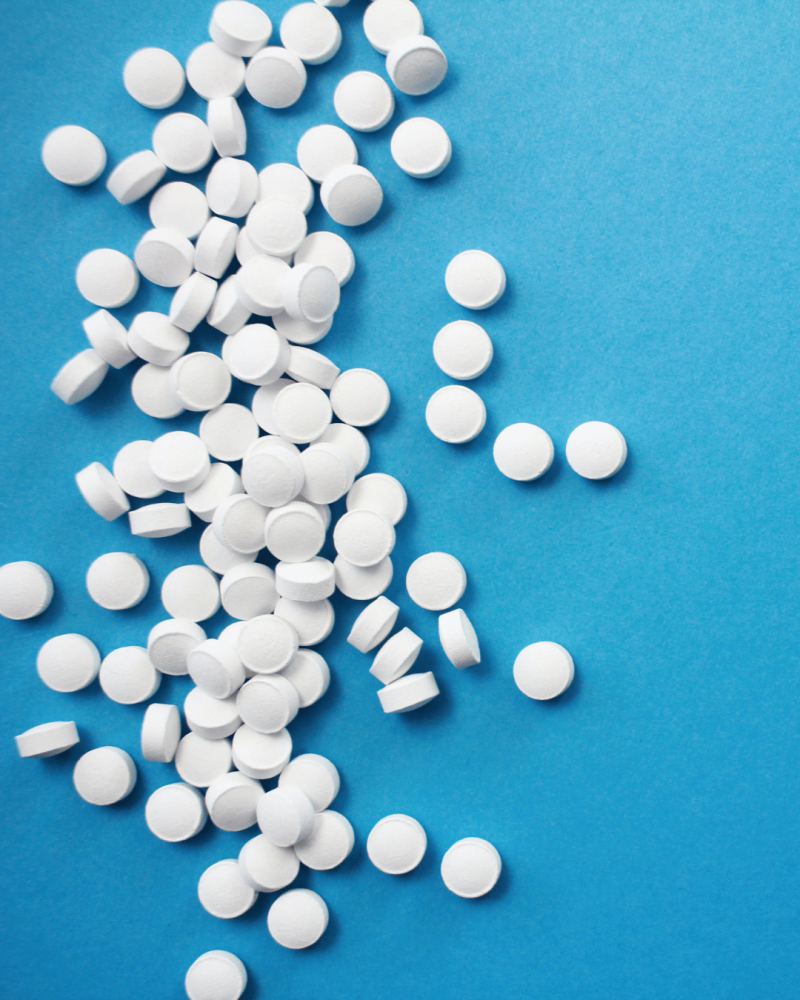
Tablet Binders Evaluation Test
There are numerous factors that affect the quality of granules These can be caused by variable process as well as the formulation, which should be constantly evaluated and monitored to determine the suitability for the tableting. Characteristics that affect the quality of granules include:
- Physical and chemical stability
- Efficacy
- Compactness
- Fast production capability
Particle Size and Distribution
The granule size affects the disintegration time, average tablet weight, variation, granule friability, drying rate kinetics of wet granulation, and granulation flowability. The formulator determines the quality of the tablet, which in turn affects the granule size and distribution. The measurements commonly used for the size and distributions include the Conductivity Test, Microscopy, and Sieving.
Tablet Surface Area
In certain instances where the drugs have limited water solubility, the surface area of the drugs is measured, usually during dissolution. Common methods used include Air Permeability and Gas Absorption.
Density
Where granules are dense and hard, higher compression load is needed to help increase the drug dissolution time and tablet disintegration. Pycnometer is usually used to determine density. The bulk density, granule, and true density can influence the porosity, flow property, dissolution, and compressibility of the tablet.
Percentage of Compressibility
Compressibility is defined as the ability of the powder to decrease in volume when subjected to pressure. It is measured by obtaining the density determination as follows:
% Compressibility = (Tapped density - Bulk density/Tapped density)*100
The compressibility measurement gives an idea on the flow property of the granules as per Carr's Index:
Carr's Index
% Compressibility | Flow Description |
5 - 15 | Excellent |
12 - 16 | Good |
18 - 21 | Fair |
23 - 28 | Poor |
28 - 35 | Poor |
35 - 38 | Very Poor |
> 40 | Extremely Poor |
Flow Properties:
Measuring the Flow Properties is important as it affects the mass of uniformity of the dose. The Flow is measured by using the Hausner Ratio or the Angle of Repose Measurement.
Hausner Ratio = Tapped Density / Bulk Density
Hausner Ratio
Hausner Ratio | Type of Flow |
Less than 1.25 | Good Flow |
1.25 - 1.5 | Moderate |
More than 1.5 | Poor Flow |
The Angle of Repose (F) is defined as the max angle between the horizontal plane and the powder surface. It is measured by the Fixed Funnel Method.
F = tan
-1
(h / r)
where, h = height of heap of pile
r = radius of base of pile
Table.12.Angle Of Repose (F)
Angle of Repose | Type of Flow |
< 25 | Excellent |
25 - 30 | Good |
30 - 40 | Passable |
> 40 | Very Poor |
Friability
The Friability is important as it affects the size distribution of the granules which in turn affects the compressibility, weight variation and granule
flowability. It is measured via the Tumbler Test or the Friability Test/Roche Friabilator and the % loss is determined.
Moisture Content
The moisture content affects the compressibility, flowability and the stability of moisture sensitive drugs and as such should be determined in order to check the granulator's quality.
For expert assistance with tablet binders, contact LFA Machines at (682) 312-0034 or email sales.usa@lfamachines.com. Our team is ready to help!